On 29 June, eco will host a German-language event to discuss the topic of “IIoT in Practice: Essential Building Blocks of Industry 4.0”. In addition to a tour of the smart manufacturing facility, experts will give keynote speeches from various perspectives on current IIoT issues. In the run-up to the event, we spoke to Michael Nicolai, Head of Sales Business Unit IT, Rittal, about digital ecosystems, smart factories and the challenges of transformation processes. Participants will learn more about this topic at the “IIoT in practice: Essential Building Blocks of Industry 4.0” event on 29 June on the premises of Rittal in Haiger. Register now for free
According to the results of a survey conducted by the opinion research institute Civey on behalf of eco Association in the run-up to the Hannover Messe, 83.7 per cent of IT experts in Germany believe that German industry is rather poorly positioned in terms of digitalisation compared to other countries. With Rittal, you are driving the development of Industry 4.0, IIoT and smart factories with your own solutions and smart services: Where do we currently stand in the field of Industry 4.0, and where do you see the major challenges for the digitisation of German industry?
Michael Nicolai: Some companies and sectors have gained very sound and very positive experience with Industry 4.0. Overall, though, we are undoubtedly still in just the first third of the journey. On the one hand, the major challenges are, first of all, to build up understanding: Understanding what you can do with data and how you can generate knowledge from data and use it to increase efficiency and flexibility in production, and understanding that we increasingly need to digitally control business processes with partners and customers across company boundaries (keyword: digital ecosystem). On the other hand, it is the expertise around the topic of Industry 4.0 itself. There is a lack of specialists in the companies who can grasp the topic and drive it forward. And it is the system landscape and infrastructure that still needs to be made fit for Industry 4.0. This involves connecting plants, devices, IT systems and people, as well as building bridges between physical and virtual worlds (keywords: IoT and digital twin).
Rittal has received several awards for the digitalisation of manufacturing at the Haiger plant with its sister company German Edge Cloud and is regarded as one of the innovation leaders in the field of Industry 4.0. Take a look into the future: In your view, which technologies will become particularly important in the field of Industrial IoT and which business challenges can they solve?
Michael Nicolai: This cannot be managed without an innovative, scalable, and agile infrastructure and technology. These were also significant evaluation criteria in the various awards we received. A so-called reference architecture for Industry 4.0, as we like to describe it ourselves, must be cloud agnostic, open to platforms, adaptable, highly available, of course, and interoperable.
This makes companies much more flexible in their actions, more efficient in production, able to produce more sustainably, and much more resilient to the ever faster-changing market influences. Especially with a view to the future, topics such as energy management, sustainability and decarbonisation will be at the top of the agenda. Without the knowledge (from data) of where I need which energy for a particular production process, for instance, I cannot identify the possible savings potential, and I cannot document and thus reduce the CO2 footprint. These are all main goals that cannot be achieved without digitalisation and digital twins. With the production, plant and product twin, we can offer three essential, industry-relevant twins within the FLG Group (which includes Rittal, Eplan, Cideon and German Edge Cloud, among others) for the implementation of a genuine smart factory in accordance with the principles of Industry 4.0.
You are hosting “IIoT in Practice: Essential Building Blocks of Industry 4.0” with Rittal. What is your personal highlight of the event and what takeaways and insights can participants expect?
Michael Nicolai: We have put a lot of thought into this, in tandem with the eco Association, and have put together a varied and perhaps somewhat unusual programme in an inspiring environment. The centrepiece and highlight will undoubtedly be the tour of the plant in Haiger, which we have developed and built according to the principles of Industry 4.0. We would like to give the participants an in-depth insight into our own progress and achievements, step-by-step on the way to a real smart factory. Furthermore, we show what challenges such a transformation process entails, and what needs to be considered. Combined with our domain and project knowledge, we can provide precious experience values for this.
Thank you very much for the interview!
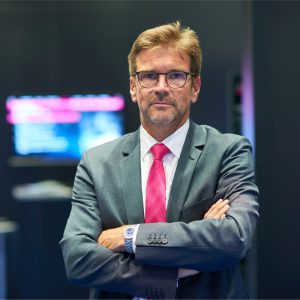